*Н.И. Гречанюк, *Л.Д. Кулак, *Н.Н. Кузьменко, **Ю.О.Смашнюк, *А.В. Демчишин, *А.Э.Фиск
*Институт проблем материаловедения им. И.Н. Францевича НАН Украины, г. Киев
** НПП «Элтехмаш», Украина, г. Винница
Рассмотрена технология получения сложно-легированных сплавов системы Ti-Nb-Zr-Si медицинского назначения. Показана возможность формирования слитков сплавов на основе титана в относительно узких диапазонах легирующих компонентов, % масc: Nb – 11-`13; Si – 0,9 - 1,1; Zr – 1,9- 2,2.
Ключевые слова: электронно-лучевая плавка, медицина, сплав титан, ниобий, цирконий, кремний.
В настоящее время в мире ведутся работы по созданию новых титановых сплавов пригодных для использования в медицине [1,2]. Новые титановые славы могут применяться взамен существующих, например, сплава Ti6Al4V, где в качестве легирующих элементов используются ванадий и алюминий. Находясь в человеческом организме в виде различных имплантатов, ионы этих вредных для человеческого организма элементов приводят к медленному токсичному отравлению. Одним из перспективных является полностью биосовместимый с человеческим организмом титановый сплав системы Ti-Nb-Si-Zr, который не содержит вредных для человеческого организма элементов [3,4]. Целью данной работы была отработка технологии получения слитков сплавов системы Ti-Nb-Si-Zr методом электронно-лучевой плавки.
Слитки сложнолегированных сплавов на основе титана, химический состав которых приведен в таблице 1, получали в Научно-производственном предприятии «Элтехмаш» (г. Винница, Украина) на промышленной электронно-лучевой установке УЭ-174, оснащённой четырьмя плоско-лучевыми пушками мощностью 60 кВт каждая.
Химический состав сплавов на основе титана
Таблица 1
№ |
Ti |
Nb |
Si |
Zr |
1 |
осн. |
11-13 |
0,9–1,1 |
1,9 – 2,2 |
2 |
осн. |
11-13 |
0,9–1,1 |
3,9 – 4,2 |
3 |
осн. |
11-13 |
0,9–1,1 |
5,9 – 6,2 |
4 |
осн. |
11-13 |
0,9–1,1 |
9,9 –10,2 |
5 |
осн. |
11-13 |
0,9–1,1 |
14,8 –15,2 |
6 |
осн. |
18-20 |
0,9–1,1 |
1,9 – 2,2 |
7 |
осн. |
18-20 |
0,9–1,1 |
3,9 – 4,2 |
8 |
осн. |
18-20 |
0,9–1,1 |
5,9 – 6,2 |
9 |
осн. |
18-20 |
0,9–1,1 |
9,9 –10,2 |
10 |
осн. |
18-20 |
0,9–1,1 |
14,8 –15,2 |
Схема рабочей камеры установки с камерой пушек, где осуществлялась плавка исходных компонентов и формирование слитков диаметром 60 мм и длиной 670-680 мм, приведена на рис. 1.
![]() |
![]() |
Рис. 1. Схема рабочей камеры с камерой пушек установки УЭ-174
В качестве исходных материалов использовали листовой титан марки ВТ 1-0, штабики ниобия НБШ–1, прутки циркония КТЦ-110, кусковой кремний КР-00. Для обеспечения качественного сплавления компонентов сплавов и однородности химического состава изготавливаемых слитков, использовали мелкие (не более 40х40 мм и толщиной 2-7 мм) куски шихтовых материалов. Процентное соотношение шихтовых материалов рассчитывали соответственно необходимого состава сплавов с учётом среднего угара титана ~5% масс.
На первом этапе равномерно перемешанную шихту помещали в промежуточную ёмкость 6, камеру 1 закрывали. После откачки воздуха и достижения необходимого вакуума в камере на уровне 10-2 Па осуществляли электронно-лучевую плавку исходной шихты в промежуточной ёмкости. Рабочий ток лучей составлял 2,4 А, ускоряющее напряжение 18 кВ. При этом для ускорения процесса использовали сразу две пушки. Две прямоугольные развертки обеспечивали проплавление шихтовой заготовки на глубину 40-60 мм. После завершения плавки и разгерметизации камеры, полученную прямоугольную заготовку (5) извлекали из промежуточной ёмкости, переворачивали на 180о и помещали в лоток механизма боковой подачи заготовок под плавку. Заготовку повторно сплавляли в промежуточную ёмкость. Одной из пушек осуществляли оплавление торца заготовки (ток луча 1,2 А), другой поддерживали прямоугольную развёртку луча по периметру промежуточной ёмкости (ток луча 2,8 А), куда поступал жидкий металл. Глубина жидкой ванны при кристаллизации металла в промежуточной ёмкости не превышала 57 мм с целью минимизации ликвации элементов сплава по массе (деление по плотности). Полученное необходимое количество заготовок-слябов (5) после двойного электронно-лучевого переплава помещали в лоток механизма подачи заготовок. Заготовки сплавляли по технологической схеме, применяемой при втором электронно-лучевом переплаве с тем лишь отличием, что жидкий металл с поверхности полностью сформированного сляба сливали в медный водоохлаждаемый тигель (7). Получаемый слиток (8) формировали на медном водоохлаждаемом поддоне (9) и вытягивали вниз с помощью механизма формирования и вытягивания слитка. Поверхность слитка (9) постоянно поддерживали в жидком состоянии (ток луча 0,9-1,1А) с целью качественного сплавления порций жидкого металла, поступаемого с промежуточной ёмкости (6). Средняя скорость вытягивания слитка составляла 5 мм/мин.
Для повышения процента выхода годного при изготовлении слитков с одинаковым содержанием ниобия использовали одну и ту же промежуточную ёмкость, в которую дошихтовывали необходимые компоненты сплава.
Таким образом, были выплавлены 10 слитков длиной 640-650 мм и диаметром 60 мм по одному для каждого химического состава. Слитки обтачивали до получения диаметра 50+3 мм и разрезали на две заготовки длиной 300+10 мм.
Химический анализ по длине и диаметру заготовок (не менее 5 измерений) проводили на мультиэлементном экспресс-анализаторе состава сплавов «EXPERT 3L» (энергодисперсионно-рентгенофлуоресцентный анализ ЭДРФА) согласно схеме pис.2.
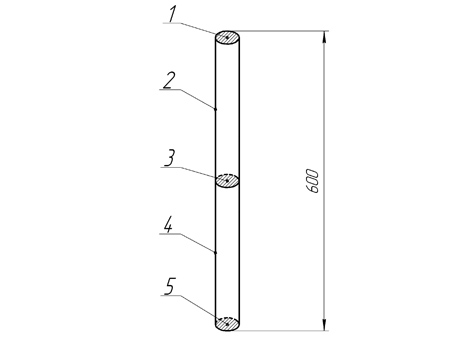
Рис. 2. Схема мест определения химического состава
Результаты анализа по двум сплавам приведены в табл. 2. Абсолютная погрешность при определении содержания (% масс.) компонентов в данном типе сплавов по титану, цирконию, кремнию и ниобию составляла соответственно: ±0,1; ±0,05; ±0,07; ±0,05.
Химический состав по длине типичного слитка, % масс.
Таблица 2
|
Точка измерения |
Ti |
Nb |
Si |
Zr |
1 сплав |
1 |
осн. |
12,67 |
1,02 |
2,19 |
2 |
осн. |
12,45 |
1,00 |
2,04 |
|
3 |
осн. |
11,94 |
0,98 |
2,24 |
|
4 |
осн. |
12,11 |
1,09 |
2,14 |
|
5 |
осн. |
12,44 |
1,08 |
2,02 |
|
2 сплав |
1 |
осн. |
20,30 |
1,06 |
1,82 |
2 |
осн. |
20,04 |
1,00 |
1,98 |
|
3 |
осн. |
19,65 |
0,90 |
1,92 |
|
4 |
осн. |
19,34 |
0,92 |
2,00 |
|
5 |
осн. |
18,88 |
0,96 |
2,05 |
Слитки не имели усадочных раковин трещин, пор, других дефектов поверхности и соответствовали требованиям технического задания заказчика. Структура слитка Ti-(18-20)Nb-(0,9-1,1)Si-(1,9-2,2)Zr представлена на рис.3,а и состоит из первичных β-зерен, по границам которых расположена силицидная фаза Ti5Si3. Внутри первичных β-зерен находится мелкодисперсная α-фаза с выделившимися по ее границам мелкодисперсными силицидами. На рис. 3,б представлено распределение кремния в характеристическом излучении Si-Кα.
![]() |
![]() |
а | б |
Рис.3. Структура слитка сплава Ti-(18-20)Nb-(0,9-1,1)Si-(1,9-2,2)Zr
Предложенная схема выплавки сплавов системы Ti-Nb-Si-Zr, с использованием на первом этапе мелких кусков шихтового материала (не более 40х40 мм и толщиной 2-7 мм), получения заготовок – слябов небольшой толщины 5-7 мм, с целью минимизации ликвации элементов по объему и применению прямоугольной развертки луча по периметру промежуточной емкости, позволила получать слитки сплавов этой системы однородные по структуре и химическому составу по длине слитка.
Исследованы механические свойства образцов из слитка сплава системы Ti-Nb-Si-Zr в литом состоянии. Вырезку образцов производили вдоль слитка с его средней части. Механические свойства сплавов в литом состоянии могут находиться в следующем диапазоне: предел прочности - 900-950 МПа, предел пластичности – 840-890 МПа, удлинение – 0,3-2,5 %, Модуль Юнга – 70-100 ГПа.
Литература
1. Патент США US 2014 105781(A1), (МПК) С22С14100, D22D 25/06. Titanium Based Ceramic Reinforced Alloy for use in Medical Implants /Fisk Andruve, Demchyshin Anatolii, Kuzmenko Mykola etc. – Опубл. 17.04.2014
2. С.В.Ладохин, Н.И.Левицкий, Т.В.Лапшук, Е.А.Дроздов, Е.А.Матвиец, М.М.Ворон Применение электронно-лучевой плавки для получения изделий медицинского назначения. Металл и литьё Украины. – №4 (263), 2015, С. 7-11.
3.Niinomi, M. Mechanicalbiocompatibility of titanium alloys for biomedical application, J. Mech. Behav. Biomed. Mater. 2008, 1, 30-42.
4. Anselme K. Human Osteoblast Adhesion on Titanium Alloy, Stainless Steel, Glass and Plastic Substrates with Same Surface Topography / K. Anselme, В. Noël, Р. Hardouin // J. Mater. Sci. Mater. Med. – 1999. – Vol. 10. – No. 12. – P.815–819.
Keywords: electron beam melting, medicine alloy of titanium, niobium, zirconium, silicon.
Annotation: The technology of producing hard-alloyed alloys of Ti-Nb-Zr-Si medical supplies. The possibility of the formation of a titanium-based alloy ingots in a relatively narrow range of alloying components, mas %: Nb - 11-`13; Si - 0,9 - 1,1; Zr - 1,9- 2,2.