Н.И.Гречанюк
Электронно-лучевоевоздействие на металлы приводящее к их нагреву, плавлению и испарению, как новое технологическое направление в области обработки материалов , интенсивно развивается с середины двадцатого столетия [ 1,2 ].
В настоящее время во всем мире ни одна отрасль промышленности связанная с получением соединением и обработкой материалов, не обходится без электронно-лучевогонагрева. Связано это с характерными преимуществами этого метода, главное из которых - возможность концентрации энергии от 103 до 5 · 108 Вт / см2 , т.е. во всем диапазоне термического воздействия, ведение процесса в вакууме, что обеспечивает чистоту обрабатываемого материала и полную автоматизацию процесса.
Развитие электронно-лучевой технологии идет в трех основных направлениях:
- плавка и испарение в вакууме для получения слитков чистых металлов, сложно легированных сплавов, покрытий, конденсированных из паровой фазы композиционных материалов [ 3,4,5 ]; используют мощные (до 1 МВт и более) электронно-лучевыеустановки при ускоряющем напряжении 20–30кВ; концентрация мощности относительно невелика (не более 105 Вт / см2);
-сварка металлов; создано оборудование трех классов: низко-, средне- и высоковольтное, охватывающее диапазон ускоряющих напряжений от 20 до 150 кВ; мощность установок составляет 1-120кВт и более при максимальной концентрации энергии 105 – 106 Вт / см2;
-прецизионная обработка материалов (сверление, фрезерование, резка); используют высоковольтные установки (80–150кВ) небольшой мощности (не более 1 кВт), обеспечивающие удельную мощность до 5 · 108 Вт / см2 .
Одновременно ведется совершенствование оборудования [ 6,7 ], источников нагрева [ 8,9 ], источников паров металлов [10] и разработка аппаратуры для наблюдения, контроля и регулирования процессаэлектронно-лучевоговоздействия. В НПП «Элтехмаш» интенсивно развивается первое из вышеперечисленных направлений. При этом особое внимание уделяется разработке и изготовлению лабораторного и промышленного электронно-лучевого оборудования для реализации целого ряда новых технологических процессов;
-осаждения теплозащитных покрытий на лопатки газовых турбин;
-получения конденсированных из паровой фазы композиционных материалов дисперсно- упрочненного микрослойного и микропористого типов;
-получение чистых металлов, специальных сплавов, ферросплавов, поликристаллического кремния солнечной чистоты для нужд машиностроения, авиастроения, энергетики, космической техники.
Защитные покрытия на лопатках газовых турбин иоборудование для их осаждения
В НПП «Элтехмаш» защитные покрытия на лопатках турбин получают путем электронно- лучевого испарения и последующей конденсации в вакууме сплавов MeCrAlY (где Me – Ni,Co, Fe) MeCrAlYHƒSiZr и керамики ZrO2 – Y2 O3 . Наряду с традиционными однослойными металлическим, двухслойнымиметалл-керамикаразработаны три варианта трехслойных теплозащитных покрытий, схемы которых приведены на рис.1.
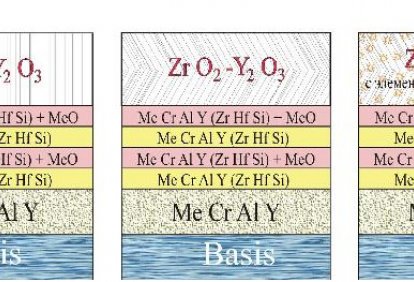
Внешний керамический слой со столбчатой структурой | Внешний керамический слой типа «зиг-заг» | Внешний керамический слой типа «зиг-заг» с элементами «саморегулирования» |
Промежуточный жаростойкий слой дисперсно-упрочненного или микрослойного типов |
Промежуточный жаростойкий слой дисперсно-упрочненного или микрослойного типов |
Промежуточный жаростойкий слой дисперсно-упрочненного или микрослойного типов |
Внутренний металлический демпфирующий слой | Внутренний металлический демпфирующий слой | Внутренний металлический демпфирующий слой |
Основа | Основа | Основа |
а | б | в |
Рис.1 Схема теплозащитных покрытий
Наиболее простым является трехслойное покрытие с внутренним металлическим (демпфирующим) MeCrAlY, MeCrAlYHƒSiZr, промежуточным композиционным MeCrAlY-MeО;MeCrAlYHƒSiZr – MeО ( где MeО Al2O3, ZrO2 – Y2 O3 ) дисперсно-упрочненного или микрослойного типа и внешним керамическим ( ZrO2 – Y2 O3 ) слоями (рис.1а) [11]. Второй вариант (рис.1б ) отличается от первого тем, что внешний керамический слой выполнен в виде«зиг-заг».
Наиболее интересным является третий вариант покрытия (рис.1в), где во внешний керамический слой ( ZrO2 – Y2O3 ), который также выполнен в виде«зиг-заг» введены частицы тугоплавких соединений. В процессе эксплуатации изделий с таким покрытием, при возникновении микротрещин во внешнем керамическом слое, частицы тугоплавких соединений, окисляясь, образуют соответствующие оксиды, которые залечивают возникшие микротрещины. Таким образом, подобное покрытие обладает эффектом «самозалечивания» или «самовосстановления».
Для реализации технологических процессов осаждения теплозащитных покрытий создано три типа промышленногоэлектронно-лучевогооборудования [ 5,6 ]. Последняя установка это универсальная промышленнаяэлектронно-лучеваяустановка для нанесения защитных металлических теплозащитных композиционных, износостойких покрытий на изделия. Схема установки приведена на рис.2. Установка представляет собой блок вакуумных камер с механизмами, устройствами и системами, обеспечивающими проведение технологического процесса нанесения покрытий на различные изделия. Снизу рабочей камеры пристыкован блок для испарения металлов, сплавов, керамики, металлоподобных соединений, в состав которого входят четыре медных водоохлаждаемых тигля и четыре механизма подачи испаряемых слитков. Четыреэлектронно-лучевыхнагревателя с холодным катодом [9] для испарения исходных материалов установлены таким образом, что каждый нагреватель может испарять материал из соседнего тигля.
Такая необходимость может возникнуть при изменении расположения или количество тиглей или требований технологического процесса. Использование электронно- лучевых нагревателей с холодным катодом способных стабильно работать начиная с вакуума 10 Па в течение 250 часов обеспечивает напуск кислорода в паровое облако из ZrO2 – Y2O3 , и получение внешнего керамического слоя теплозащитного покрытия стехиометрического состава.
Для нагрева покрываемых изделий служат такие же две электронные пушки, установленные сверху технологической камеры.
Две шлюзовые камеры предназначены для перегрузки покрываемых изделий. Разобщение объемов камер проводится двумя вакуумными затворами.
В шлюзовых камерах предусмотрены устройства ионной очистки изделий перед нанесением покрытий.
Наличие двух вспомогательных камер обеспечивает непрерывный цикл нанесения покрытия так как нанесение покрытий на изделия, подаваемые поочередно из шлюзовых камер происходит без развакуумирования рабочей камеры.
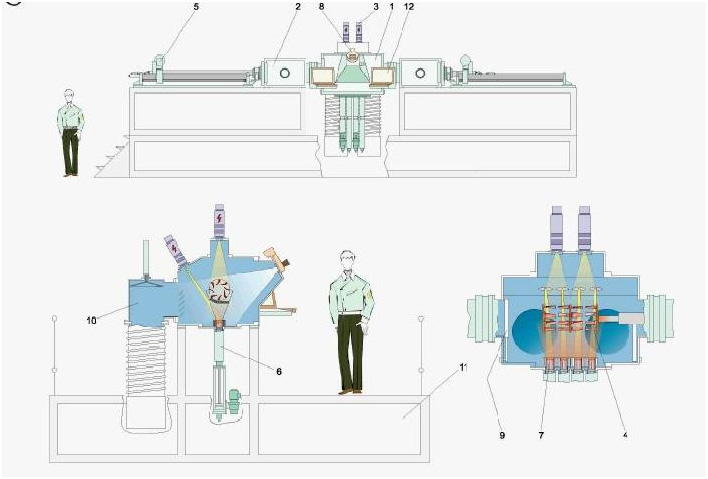
Рис.2
1.Камера технологическая, 2. Камера шлюзовая, 3. Электронная пушка, 4. Кассета, 5. Механизм подачи кассеты (изделия) 6.Механизм подачи слитка, 7. Тигель, 8. Смотровая система, 9. Заслонка, 10. Вакуумная система, 11. Площадка обслуживания, 12.Пульт управления
Вконструкции установки использованы источники питания для каждого электронного нагревателя с ускоряющим напряжением 30 кВ. Это обеспечивает постоянный уровень ускоряющего напряжения и стабильность электронного пучка во время ведения технологического процесса.
Система управления установки осуществляет:
-контроль технического состояния всех систем установки;
-автоматическую подготовку установки к выполнению технологического процесса;
-управление с пульта оператора узлами установки при проведении процесса;
-сбор, обработку, отображение в реальном масштабе времени и хранение технологических параметров и циклограммы процесса;
Применение одного из трех типов промышленногоэлектронно-лучевогооборудования для осаждения покрытий определяется конкретными технологическими задачами. Для их решения создан замкнутый цикл осаждения покрытий, включающий выплавку всех типов слитков на никелевой, кобальтовой и железной основах в соответствии с ТУ У27.4-20113410-001-2001,использование штабиков керамики ТУ У13.2-20113410-004-2003.
Композиционные материалы для электрических контактов и оборудование для их получения
Разработка конденсированных из паровой фазы композиционных материалов для электрических контактов не содержащих благородных металлов осуществляется в трех направлениях:
а) композиционные материалы для разрывных контактов; б) материалы для скользящих контактов; в) материалы для контактов вакуумных выключателей.
Серьезным научным достижением является разработка научных основ формирования микрослойных материалов в том числе и для электрических контактов с толщиной чередующихся слоев меньше 0,5 мкм при температуре более 0,3 температура плавления наиболее легкоплавкого из испаряемых материалов Как известно [13], до последнего времени подобные материалы получали методомэлектронно-лучевого испарения и последующей конденсации металлов и неметаллов в вакууме при температуре подложки не выше 300°С. На базе данных исследований впервые в мировой практике разработана промышленная электронно-лучеваятехнология получения толстых (до 5 мм) микрослойных материалов (Cu-Zr-Y) Mo для разрывных контактов [14-16]. Новые композиты получившие название «Материалыдисперсно-упрочненныедля электрических контактов (МДК)» сертифицированы и выпускаются согласно техническим условиям ТУУ20113410.001-98. Основное достоинство материалов МДК отсуствие в их составе серебра, поэтому они в 2,5 ÷ 3 раза дешевле по сравнению с порошковыми электроконтактами, а по эксплуатационной надежности превосходят существующие материалы для электрических контактов в 1,5 ÷ 2 раза.
Одновременно с промышленным внедрением материалов для разрывных контактов совместно с институтом проблем материаловедения академии наук Украины, Вроцлавским политехническим институтом (республика Польша) ведутся работы по созданию материалов на основе меди, хрома, вольфрама, углерода для скользящих контактов [17] и контактов дугогасительных камер [18-20].
Промышленные технологииэлектронно-лучевогопереплава металлов, сплавов
и оборудования для их осуществления.
Освоены промышленные технологии:
-электронно-лучевого переплава отходов быстрорежущих сталей и получение товарных слитков для последующего изготовления из них инструмента[21-22];
-получение сплавов на кобальтовой, никелевой основах для последующего нанесения защитных покрытий;
-получения высокочистой меди для использования в атомной энергетике, формирования сложнолегированных титановых сплавов;
-получения высокочистых благородных металлов и сплавов на их основе [23-24].
В последнее время создан ряд специализированных промышленныхэлектронно-лучевыхустановок для получения товарных слитков и слябов размерами: круг от 60 до 400 мм; квадрат 60х60 до 400 мм и длиной до 3 метров.
В данных установках впервые использованы новые высоковольтные источники питания разработанные совместно НПП «Элтехмаш» и ОАО «Укрэлектроаппарат» (Украина) и электронно-лучевые газорязрядные нагреватели, разработанные под руководством В.И.Мельника [9].
Поисковые работы
Электронно-лучевая технология получения поликристаллического кремния солнечной чистоты. Глобальное ухудшение климата, резкое уменьшение мировых запасов нефти и газа заставляет ученых интенсивно развивать исследования в области развития нетрадиционных видов энергии. Наиболее перспективным направлением является использование систем прямого преобразования световой энергии солнечного излучения в электричество. Преимущества фотоэлектрических систем (ФЭС) прямого преобразования состоят в том, что не имеют движущихся механических частей, не нуждаются в воде или другом теплоносителе и поэтому требуют минимального обслуживания [25].
Доминирующий материал для массового производства ФЭС - кремний [26]. Характеристики эффективности солнечных элементов на основе кремния сравнительно высоки, сырье для получения кремния (диоксид кремния SiO2 : кварц, кварцевые руды, кварцевые пески) достаточно распространено и доступно. Имеются мощные производства кремния «металлургического» качества.
Из-занизкой экологичности, ввиду высокой и чрезвычайной дороговизны сырья, весьма мала вероятность организации масштабного производства ФЭС на базе других веществ, таких как CaAs, CdS, CdТe, CuInSe, TnP и другие [27].
Существует несколько кремниевых материалов на основе которых производится подавляющее количество солнечных элементов. Основные из них:
-монокристалический кремний МК-Si в виде круглых пластин толщиной 200 ÷ 500 мкм, которые получают резкой слитков, выращиваемых способами Чохральского или бестигельной зонной плавки;
-поликристаллический кремний ПК- Si в виде прямоугольных пластин, получаемых резкой крупных литых блоков кремния;
-поликристалический кремний Л- Si в виде прямоугольных пластин, получаемых непосредственно из расплава путем машинного литья плит или листов;
-аморфный гидрогенизированный кремний Ca-Si:Н осаждаемый из газовой фазы в виде тонких ( ~ 1 мкм) пленок на подложку в процессе разложения моносилана SiH4 ;
-тонкопленочный микрокристаллический кремний МК-Si , получаемый осаждением из газовой фазы.
Дали использования a – Si:H;MK-Si;nk-Siвместе с Л- Si в общемировом производстве солнечных элементов в 1990 ÷ 1993 гг. были приблизительно одинаковыми [29].
Традиционное производство высокочистого кремния является достаточно сложным энергоемким и включает несколько этапов:
1. Добыча чистого кварца;
2. Выплавка металлургического (технического) кремния (м- Si ) ;
3. Получение и очистка кремнийсодержащих газов (силанов);
4. Производство высокочистых поликристалических стержней (n - Si );
5. Выращивание монокристалических слитков(MK-Si) .
Имеющиеся данные показывают, что для производства солнечных элементов может быть использован металлургический кремний как с дополнительной очисткой так и без нее [25]. Весьма перспективным, альтернативным химическим методом получения высокочистого поликристалического кремния являетсяэлектронно-лучевоерафинирование технического (металлургического) кремния [ 30 ]. Схема промышленной электронно-лучевой установки для рафинирования технического (металлургического) кремния приведена на рис.3.
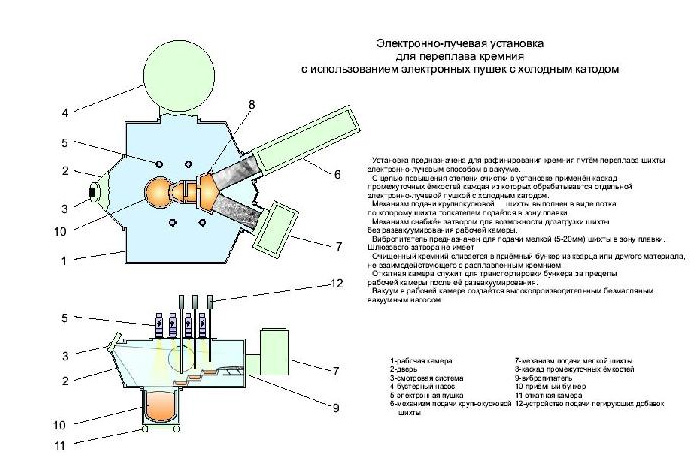
Рис.3
Установка снабжена соответствующими механизмами и устройствами, обеспечивающими получение до 800 кг рафинированного кремния за 8 часов. Установка снабжена тремя промежуточными емкостями (позиция 8), в которых осуществляется расплавление, перегрев и рафинирование кремния. Рафинированный кремний сливается в специальный тигель где осуществляется направленная кристаллизация жидкого расплава.
Проведение рафинирования кремния последовательно в каждой из трех промежуточных емкостей осуществляется отдельнойэлектронно-лучевойпушкой мощностью 100 кВт. Подача модификаторов для рафинирования кремния осуществляется с помощью дозаторов 12.
Установка снабжена двумя механизмами подачи исходной шихты в зону плавки (позиция 6,7 ). Механизм 6 предназначен для подачи крупной кусковой шихты. Механизм снабжен затвором для дозагрузки шихты без развакуумирования рабочей камеры. Механизм 7 оснащен вибропитателем для подачи в зону плавки мелкой (5 ÷ 20мм ) шихты.
Электронно-лучеваятехнология получения мишеней для магнетронного распыления
Освоена технология получения путем испарения и последующей конденсации в вакууме мешеней из хрома для магнетронного распыления.
Внешний вид мишеней показан на рис.4.
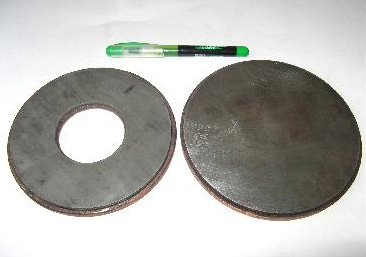
Рис.4
Электронно-лучевая технология получения композиционных порошков.
Проведены исследовательские работы по получению металлических, керамических и композиционных порошков. Процессы испарения и конденсации в вакууме позволяют получать практически любые типы порошков размером от 0,05 до 1,2 мкм с производительностью до 15 кг порошка в час.
Схема установки для получения порошков приведена на рис.5.
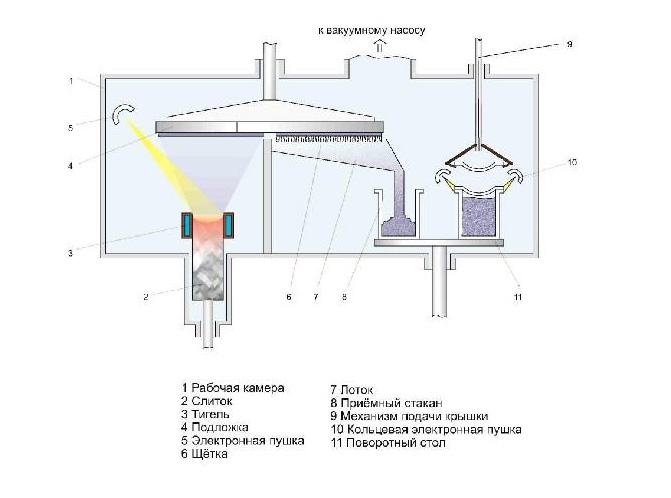
Рис.5
В соответствии с техническим процессом конденсация парового потока осуществляется на охлаждаемую вращающую подложку. С помощью специального скребка порошок снимается с подложки и по специальному лотку перемещается во вспомогательную камеру, где размещена специальная емкость для приемки порошка. После заполнения емкости осуществляется ее вакуумирование. Порошок в емкости извлекается из вспомогательной камеры и передается для дальнейшего использования.
Литература
1. Мовчан Б.А., Малашенко И.С. Жаростойкие покрытия осаждаемые в вакууме. – Киев: Наукова думка, 1983 – 230с.
2. Зуев И.В. Обработка материалов концентрированными потоками энергии. – Москва: МЭИ, 1998 – 162с.
3. Мовчан Б.А., Тихоновский А.Л., Курапов Ю.А. Электронно-лучевая плавка металлов и сплавов – Киев: Наукова думка, 1973 – 230с.
4. Гречанюк Н.И., Кучеренко П.П., Осокин В.А., Шпак П.А. Современное состояние и перспективы состояния теплозащитных покрытий для лопаток газотурбинных установок и оборудование для их нанесения . Новини енергетики.
5. Гречанюк Н.И., Осокин В.А., Гречанюк И.Н. Новые композиционные материалы для електрических контактов и способ их получения. Рынок металлов № 4, 1999 – с.58-60.
6. Pat. US 6, 923, 868 BZ Installation for elektron – ray coatication of coatings I.M.Grechanyk. P.P.Kucherenko. – Publ. 02.08/2005/
7. Пат. 2265078 РФ. Установка для электронно-лучевого нанесения покрытий / Н.И.Гречанюк, П.П.Кучеренко. – Опубл. 12.27.2005
8. Патент Украины № 40664. Електронна гармата з лінійним термокатодом для електронно- променевого нагрівання. / Гречанюк М.І., Кучеренко П.П., Піюк Є.Л., Опубл. № 7 2001р.
9. Denbnovetskiy SV, Melnik V.G. Melnik I.V., Tygay B.A. Application of Glow Discharge Electron Guns for Plasma Activated Deposition of Coatings / Електротехника и електроника . 5-6 2006 с.115 – 118.
10. Залкин А.С. Источники паров металлов для научных исследований и технологий. – Новосибирск: Институт теплофизики РАН, 1992 75с.
11. Патент Украины № 42052. Защитное покрытие для лопаток газовых турбин. / Н.И.Гречанюк , П.П.Кучеренко, В.А.Осокин, И.Б.Афанасьев, С.С.Белик, В.А.Акрымов, И.Н.Гречанюк. Опул.в Бюл. № 9 2001г.
12. Патент 2271404 РФ. Способ получения микрослойных термостабильных материалов. / Н.И.Гречанюк – Опубл.03.10.2006г.
13. Иявинский А.И. Структура и прочность слоистых и дисперсно-упрочненных пленок. – М: Металлургия 1986 – 140 с.
14. Патент Украины 34875. Композиционный материал для электрических контактов. / Н.И.Гречанюк, В.А.Осокин, И.Б.Афанасьев. Опубл.в Бюл. изобр. № 2 – 2001 г.
15. Grechanyk N.I., Osokin V.A., Grechanyk I.N. Vinakova R.V. Composite materials on base of copper and molybdenum, condensed from vapor phnse, for electrik contacts. Structure, properties, technology. Part 1. State – of – the art and prospects of application of technology of elekctron beat high-rateevaporation-condensation for producing materials of elektrik contakts. Advances in Electrometallurgy № 2, 2005 p.24-29.
16. Grechanyk N.I., Osokin V.A., Grechanyk I.N., P.P.Kucherenko, Vinakova R.V. Golovkova M.E., Kopylova G.E. Covposite materials on base of copper and molybdenum, condensed from vapor phase, for electric contacts. Structure, properties, technology. Part 2. Fundamentals of electron beam technology for producing materials for electric contacts.
17. Miedzinski B., Okraszcwsky Z, Grechanyk N, Wandzio J. Performance of sliding contacts with Cu-Mo layers for transportation in mining industry. Электрические контакты и электроды. Сборник трудов ИПМ НАНУ Киев 2008с.150-155.
18. Патент Украины № 32368А. Контактный материал для дугогасительных камер и способ его получения. / Н.И.Гречанюк, Н.И.Плащенко, В.А.Осокин, И.Б.Афанасьев, И.Н.Гречанюк. Опубл. в бюл. избр. № 7 –11 15.12.2000.
19. Патент Украины № 76737. Контактная система вакуумной дугогасительной камеры. / Н.И.Гречанюк, Н.Н.Плащенко, А.В.Зварич, В.А.Осокин. Опуб. в Бюл.избр. № 9 2006.
20. Решение № а 200703343 о выдачи Патента Украины от 29.11.2008. Композиционный материал для электрических контактов и электродов. / Н.И.Гречанюк, И.Н.Гречанюк, В.А.Денисенко, В.Г.Гречанюк.
21. Шпак П.А., Гречанюк В.Г., Осокин В.А. Влияние электронно-лучевого переплава на структуру и свойства быстрорежущей стали Р6М5. / Проблемы спец.электрометаллургии –2002 - № 3 – с.14-17.
22. Патент Украины 37658. Способ изготовления заготовок для инструмента из быстрорежущей стали. / Н.И.Гречанюк, И.Б.Афанасьев, П.А.Шпак. Опубл. в Бюл. избр. № 7 2003.
23. Савенко В.А., Гречанюк Н.И., Чураков О.В. Электронно-лучевое рафинирование в производстве платины и сплавов на ее основе. Сообщение 1.Электронно-лучевое рафинирование платины. / Современная электрометаллургия-2008 - № 1–с.16-18.
24. Савенко В.А., Гречанюк Н.И., Чураков О.В. Электронно-лучевое рафинирование платины и сплавов на ее основе. Сообщение 2.Электронно-лучевое рафинирование сплавов на основе платины. / Современная электрометаллургия – 2008 - № 3 -с.38-41.
25. Басин А.С., Шишкин А.В. Получение кремниевых пластин для солнечной энергетики. РАН Новосибирск 2000, 390с.
26. Rohatgi A., Weber E.R., Kimerling L.C. Opportunities in Silicon photovoltaics and defect control in photovoltaic materials. / J.Electron. Mater – 1993 – Vol. 22, № 1. – p 65-72.
27. Shan A., Meier T., Tsharner R., Wyrsch N. Photo-Voltaic power generation. / Plasma phys and Controlled Fusion. – 1992 – Vol 34. № 13, - p1837-1844.
28. Eyer A., Kauber A., Goetzberger A. Silicon sheet materials for solar cells. / Optoelectronics Devices and Techol. – 1990. – Vol. 5, № 2 –p239-257.
29. Surek T. NREL PV prodram overview. / Naticnal Renewable Energy laboratory. – G olden, Colorado, USA., 1955 – 15p.
30. Grechanyk N.I., P.P.Kucherenko, Grechanyk I.N. New electron beam eguipment and technologies of producing advanced materials and coatings. / Paton Welding Jornal – may 2007 –p 25-29.