Сучасний стан та перспективи використання технології високошвидкісного електронно-променевого випаровування і наступної конденсації в вакуумі металів і неметалів для отримання матеріалів електричних контактів і електродів
Modern station and promises of application of technology electron- beamevaporation-condensationmetals non metals in vacuum for resaving of materials for electrical contacts and electrodes
© Н. И. Гречанюк, Р. В. Минакова, О. П. Василега, Г. Е. Копылова, И. Н. Гречанюк*, Б. Медзинский**
© N. I. Grechanyuk, R. V. Minakova, O. P. Vasilega, G. E. Kopulova, I. N. Grechanyuk, B. Miedzinski
Институт проблем материаловедения им. И. Н. Францевича НАН Украины, Киев
*НПП “Элтехмаш”, Винница, Украина, **Вроцлавский технический университет, Польша
Представлены результаты изучения структурных особенностей конденсированных композиционных материалов на основе меди и тугоплавких металлов (W, Мо, Cr) и их свойств. Установлено, что характерной особенностью этих конденсированных материалов является слоистая структура с иерархией слоев на макро-,микро- и субмикроуровнях. Для конденсированных материалов на основе меди и хрома отмечены образование и распад пересыщенных твердых растворов на основе хрома. Приведены примеры практического применения конденсированных из паровой фазы композиционных материалов Cu—Mo, Cu—W, Cu—Cr, Cr—Al2O3 для изготовления электрических контактов и электродов.
Наведено результати вивчення структурних особливостей конденсованих композиційних матеріалів на основі міді та тугоплавких металів (W, Мо, Cr) і їх властивостей. Встановлено, що характерною особливістю цих конденсованих матеріалів є шарувата структура з ієрархією шарів на макро-,мікро- и субмікрорівнях. Для конденсованих матеріалів на основі міді і хрому спостерігається утворення і розпад пересичених твердих розчинів на основі хрому. Наведено приклади практичного використання конденсованих із парової фази композиційних матеріалів C—Mo,Cu—W,Cu—Cr,Cr—Al2O3для виготовлення електричних контактів і електродів.
In this article principle schemes of equipment and technological process of condensate composite materials in systems Cu—Y—Zr—(W,Mo, Cr) making were given. It was established that besides of mentioned in special literature atom–molecularmechanism of mass transfer the drop mechanism is evident. This mechanism determines of structure peculiarities of condensates containing W, Mo, Cr with different interaction with Cu. The investigating condensates advantage by laminates structure with hierarchy of macro-,micro- and sub micro levels and with effects of age-hardeningand dispersion- strengthened of material. However the decomposition of non-equilibriumsolid solutions on Cu and Cr base requires suitable sampling of technological process parameters to suppress of the structure and element distribution irregularity. Examples of practical application of condensed from the vapor phase composite materials of Cu—Mo,Cu—W,Cu—Cr,Cu— AI2O3 for the manufacture of electrical contacts and electrodes were reduced.
Ключевые слова: электронно-лучевое испарение-конденсация,оборудование, технология, структура, свойства, применение.
Ключові слова: електронно-променеве випаровування-конденсація,обладнання, технологія, структура, властивості, використання.
Keywords: еlectron-beamevaporation-condensation, equipment, technology, structure, properties, application.
Испарение и последующая конденсация материалов в вакууме — относительно новое направление в материаловедении [1]. Упоминание о нем относится к началу 70-х годов, развитие прогрессирует. В его основе использование физико-технологических свойств электронного луча, отличающегося наиболее высокой эффективностью при металлообработке по сравнению с другими известными концентрированными потоками энергии (лазером, плазмой). Электронный луч имеет наибольший коэффициент поглощения энергии. Диапазоны мощности и концентрации энергии в луче значительны (мощность электронных лучей — 1 МВт и более). В связи с этим нагрев материала до заданных температур плавления-испарения происходит с очень высокими скоростями.
Электронно-лучевое высокоскоростное испарение с последующей конденсацией в вакууме является одним из составляющих техноло- гического процесса получения тонких (до 5 мкм) пленок для радиотехники, микроэлектроники, вычислительной техники и др. [2], а также толстых (более 5 мкм), используемых в качестве эффективных защитных и износостойких покрытий [3—8].
Прогнозная оценка мирового производства металлических материалов с использованием различных технологических процессов (традиционной металлургии и осаждения из паровой фазы, включая тонкие пленки, получаемые магнетронным распылением металлических мишеней) до 2010 г. свидетельствует о дальнейшем росте производства новых материалов, получаемых осаждением паровой фазы в вакууме [9].
Перспективным является создание многокомпонентных покрытий, предназначенных для повышения эрозионной стойкости электрических контактов коммутационных аппаратов. Научный и производственный опыт, приобретенный при разработке покрытий из сплавов на основе меди, легированных оловом, хромом, алюминием, никелем и титаном, обобщен в монографии [10].
О возможности применения высокопрочных пленок системы Сu— 0,5% Al2O3 в качестве покрытий изделий электротехнического назначения отмечается в работе [11]. Важно подчеркнуть, что осажденные в вакууме покрытия значительно превосходят соответствующие гальванические по уровню износостойкости, особенно ее температурной стабильности.
Несмотря на очевидные преимущества, вакуумные покрытия не всегда экономически оправданы, поскольку коэффициент использования пара обыч- но не превышает 20%. Однако из-за разности в упругости паров компонентов возникают непреодолимые трудности при испарении из одного источника материалов на основе меди или серебра с добавками тугоплавких металлов вольфрама, молибдена, тантала, ниобия, циркония, гафния в том или ином соотношении, соответствующем составу современных электроконтактных материалов.
Как известно, традиционными методами получения композиционных материалов (КМ) для электрических контактов являются методы порошковой металлургии. Технологические особенности изготовления материалов для электрических контактов, их эксплуатационные характеристики и области применения освещены в публикациях [12—18].
Несмотря на широкий выбор материалов для электрических контактов различного назначения, проблема создания высоконадежных электрических контактов так до конца и не решена, поскольку требования, предъявляемые к материалу контактов, зависят от типа коммутационного аппарата и изменяются по мере его совершенствования и замены новым. Удовлетворить эти требования могут материалы, характеризуемые опти- мизированной структурой и соответствующим комплексом свойств, обеспечивающих формирование в рабочем слое вторичной структуры с повышенными электроэрозионной стойкостью, сроком службы и надежностью контактов.
Определяющее влияние на эксплуатационные характеристики материалов электрических контактов оказывает также структурный фактор исходных материалов. Повышение дисперсности КМ в системах Ag—Me, Ag—MeO, способствующее снижению интенсивности плазменных потоков, увеличивает электроэрозионную стойкость средненагруженных и слаботочных контактов из этих материалов [19].
Процессы испарения и конденсации позволяют конструировать материал на атомно-молекулярном уровне. В этой связи значительный научный и практический интерес представляет использование высокоскоростного электронно-лучевого испарения и последующей конденсации металлов и неметаллов в вакууме для получения массивных конденсированных КМ для электрических контактов. Лабораторные образцы толщиной 1—2мм дисперсно-упрочненного и микрослойного типов с 1970-х годов исследуются в Институте электросварки НАН Украины [20], в Королевском авиационном научно-исследовательском институте Министерства обороны Великобритании [21] и в ряде других научно-исследовательских лабораторий. Однако о серийном выпуске подобных материалов до последнего времени ничего неизвестно.
Прежде чем приступить к разработке электронно-лучевой технологии изготовления КМ для электрических контактов, необходимо решить ряд прикладных и научных задач, одной из которых является экономическая. По стоимости электроконтактные материалы, получаемые испарением и последующей конденсацией в вакууме, должны быть сопоставимы с подобными материалами, изготавливаемыми методами порошковой металлургии. Наибольший интерес представляют разработка и использование для электрических контактов КМ, не содержащих драгоценных металлов. По эксплуатационной надежности конденсированные электроконтактные материалы не должны уступать спеченным порошковым композициям. Для этого необходимо решить вопросы выбора составов и структуры электроконтактных материалов, оптимизации их физико-механических характеристик, разработки технологических условий и создания воспроизводимой промышленной технологии изготовления КМ.
Материалы, получаемые методами порошковой металлургии без драгоценных металлов, довольно широко распространены в производстве контактов коммутационных аппаратов. Порошковые КМ этих контактов содержат 20—80% (мас.) тугоплавкой составляющей, а легкоплавкой является медь. Технологическими добавками могут быть никель и кобальт, функциональными — некоторые оксиды, бор и другие элементы и соединения. В промышленности в основном применяют КМ с содержанием 50 и 70% W(Mo) [14, 22].
При использовании контактов из материалов в системе W—Cu продуктами окисления чаще всего являются оксиды WO3 и Cu2O [18, 23]. Их удельное сопротивление изменяется в достаточно широких пределах: для WO3 — от 1 (при сильном отклонении) до 1·1012 Ом/см (при стехиометрическом составе), для Cu2O — соответственно от 1·103 до 1·1010 Ом/см.
При коммутации тока на воздухе подобные процессы наблюдаются и в рабочем слое контактов из псевдосплавов Mo—Cu.Молибден и медь растворимы ограниченно [24], в то время как их оксиды взаимодействуют и образуют стойкие соединения (CuMoO4, Cu3Mo2O9 и др.) [25, 26]. При температуре выше 700 ºС возникает легкоплавкая эвтектика в системе MoO3—Cu2O. Установлено, что оксидная пленка, имеющая состав эвтектики в этой системе, легко растекается по поверхности контакта, заполняя неровности [25, 26]. Отслаиваясь после кристаллизации от поверхности контакта из-за слабой адгезии, пленка способствует эффекту “самозачистки” и снижению уровня переходного сопротивления контактной пары [22].
Металлы и КМ, предназначенные для работы в окислительных средах, защищают от окисления посредством легирования либо нанесения покрытий. Исходя из особенностей влияния добавок на электропро- водность легированных сплавов на основе меди [14] и коррозионную стойкость [27], для дополнительного легирования КМ на основе меди и молибдена с целью улучшения их функциональных характеристик выбраны цирконий и иттрий. Далее представлены результаты разработки основ электронно-лучевой технологии получения конденсированных из паровой фазы КМ Cu—Zr—Y—Moдля разрывных и скользящих электрических контактов, работающих на воздухе, Cu—Zr—Y—Сr, Cu— Zr—Y—W — для контактов дугогасительных камер, Cu—Zr—Y—Al2O3 для электродов контактной сварки.
Для получения электроконтактных материалов, конденсированных из паровой фазы, использовали промышленную электронно-лучевую установку, разработанную научно-производственным предприятием “Элтехмаш” (г. Винница, Украина). Общий вид и схема установки приведены на рис. 1 и 2, технические характеристики — в табл. 1.
Установка представляет собой сложный агрегат, состоящий из рабочей камеры (рис. 2, поз. 1), камеры пушек (рис. 2, поз. 2), системы питания, управления, обеспечения вакуума и т. д. В нижней части рабочей камеры расположены четыре механизма (рис. 2, поз. 8) с медными водоохлаждаемыми тиглями, два из которых диаметром 100 мм, два других — диаметром 70 мм. Длина штоков нижних механизмов такова, что позволяет размещать в тиглях слитки длиной до 800 мм. К боковой части рабочей камеры 1 пристыкована камера пушек 2. Четыре электронно-лучевые пушки, расположенные сверху и снизу, предна- значены непосредственно для подогрева подложки, другие четыре — для испарения исходных материалов.
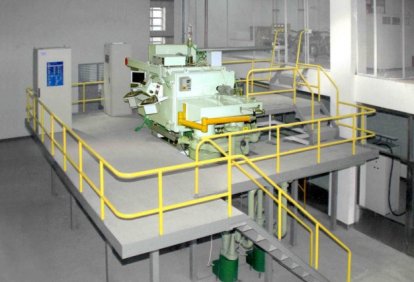
Рис. 1. Общий вид промышленной электронно-лучевой установки Л-5 для получения материалов и сплавов.
Исходными материалами для получения конденсированных из паровой фазы КМ служили слитки меди ∅ 98,5 мм и длиной 500 мм; слитки молибдена и вольфрама ∅ 68,5 мм и длиной 500 мм после электронно-лучевого переплава; слитки хрома ∅ 68,5 мм и длиной 300 мм, полученные индукционным переплавом в секционном кристаллизаторе электролити- ческого хрома в среде очищенного аргона; иттрий марок ИТМ1, ИТМ2; цирконий, изготовленный в соответствии с техническими условиями ТУ 5-20-069-85. Штабики оксида алюминия диаметром 68,5 мм и длиной 50 мм получали из порошка марки ХЧ (химически чистый) холодным прессованием и последующим спеканием на воздухе при температуре 1500 ºС. Чистота всех исходных испаряемых материалов была не ниже 99,9%.
Технологический процесс осаждения композиционных материалов проводили следующим образом (рис. 2). Подложку 3, выполненную в виде диска диаметром 1000 мм, закрепляли на механизме подвески и вращения изделия 7. Поверхность подложки, на которую осуществлялась конденсация, обрабатывали по 9—10 классу чистоты. Для легкого отделения сконденсированного материала от подложки на последнюю предварительно осаждали тонкий (10—15 мкм) разделительный слой из фторида кальция СаF. В два из четырех медных водоохлаждаемых тигля диаметром 100 мм (рис. 2, поз. 5) помещали слитки малолегированного сплава на основе меди Cu—Zr—Y с суммарным содержанием легирую- щих добавок (Zr, Y) до 0,2% (мас.). В два других, диаметром 70 мм, помещали слитки молибдена, вольфрама, хрома, а также керамические штабики оксида алюминия при получении материала в системах Cu—Zr—Y—Mo, Cu—Zr—Y—W, Cu—Zr—Y—Cr и Cu—Zr—Y—Al2O3 для разрывных, скользящих, вакуумных контактов и электродов контактных сварочных машин соответственно.
Блок камер вакуумировали. После достижения глубины вакуума (1,3—4)·10-2 Па включали электронно-лучевые пушки. С их помощью подложка, на которую осуществлялась конденсация пара, нагревалась до температуры 700 ± 20 ºС. Параллельно прогревали поверхность исходных (испаряемых) слитков, доводя их до расплавления и испарения. Длительность технологического процесса получения листовых заготовок КМ толщиной 2—4мм и диаметром 1000 мм в зависимости от требуемой толщины заготовки составляет 3—5ч. Конденсат отделяется от подложки, рубится на заготовки, которые затем напаиваются на контактодержатели или заготовки электродов для контактной сварки.
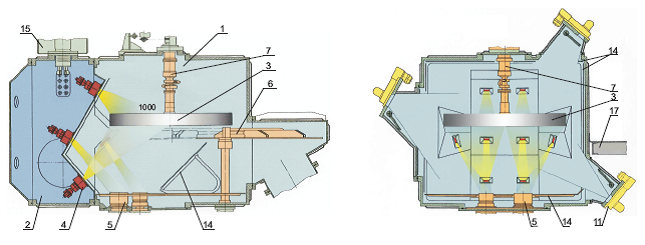
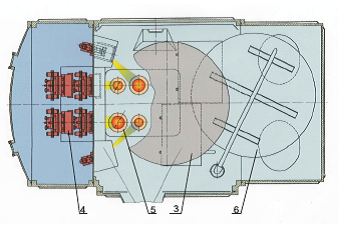
Рис. 2. Схема промышленной электронно-лучевой установки Л-5 для получения материалов и сплавов: 1 — рабочая камера; 2 — камера пушек; 3 — изделие; 4 — электронные пушки; 5 — блок тиглей; 6 — заслонка; 7 — механизм подвески и вращения изделия; 8 — механизмы подачи слитков; 9 — вакуумная система; 10 — система охлаждения; 11 — смотровая система; 12 — пульт управления; 13 — шкафы управления; 14 — экраны; 15 — высоковольтный ввод; 16 — манипулятор; 17 — площадка обслуживания.
Т а б л и ц а 1. Технические характеристики промышленнойэлектронно-лучевой установки Л-5 для получения материалов и сплавов
Значение | Параметр |
Установленная мощность, кВт | 480 |
Напряжение питающей трехфазной сети промышленной частотой 50 Гц, В | 380 |
Ускоряющее напряжение электронно-лучевых пушек, кВ | 20 |
Количество и номинальная мощность электронных пушек n x кВт |
8x60 |
Диаметр напыляемой подложки, мм | до 1000 |
Толщина конденсата, мм | 0,1-5 |
Скорость конденсации, мкм/мин: для металла для керамики |
До 50 до 5 |
Количество тиглей*, шт - диаметром 100 мм - диаметром 70 мм |
2 2 |
Длина испаряемых слитков, мм | 500 |
Скорость подачи слитков, мм/мин | 0,28-280 |
Грузоподъемность механизма подвески и вращения изделия, кг, не более | 100 |
Масса установки (ориентировочно), т | 20 |
Площадь, занимаемая установкой, м2 | 80 |
Уровень рабочего вакуума в технологической камере, Па | 6·(10-2-10-3 |
Давление охлаждающей воды, Па | (3-4)·105 |
Расход охлаждающей воды (при t = 15 °C), м3/ч | 12 |
*Тигли взаимозаменяемы и могут быть расположены в любой последовательности.
Наибольшее промышленное применение нашли конденсированные из паровой фазы КМ системы Cu—Zr—Y—Moдля разрывных и скользящих электрических контактов [28]. Материалы, получившие название МДК, сертифицированы и выпускаются согласно техническим условиям Украины ТУ У 20113410.001-98. Технология их изготовления защищена патентами Украины [29, 30]. Физико-механические свойства конденсированных материалов Cu—Zr—Y—Moприведены в табл. 2. Из табл. 2 следует, что указанные материалы отличаются достаточно высокой твердостью, прочностью, электропроводностью и удовлетворительной пластичностью.
Поверхность конденсатов и сечения образцов, параллельные и перпендикулярные паровому потоку, изломы материала (после механических испытаний), а также поверхность и сечения контактов коммутационных аппаратов (после стендовых и натурных испытаний) подвергали микроструктурным исследованиям.
Т а б л и ц а 2. Физико-механические свойства КМ Cu—Zr—Y—Mo
Материал |
Химический |
Плотность |
Удельное |
Микро |
Механические свойства | |||
до отжига |
после отжига, |
|||||||
σ в, МПа |
δ, % |
σ в, МПа | δ, % | |||||
МДК-1 |
Cu—3—5Mo |
8,9—9,0 | 0,021—0,022 | 1000—1500 |
300—430 |
10,3—7,3 | 295—420 | 17,6—9,5 |
МДК-2 | Cu—5,1—8Mo | 9,0—9,05 | 0,022—0,024 | 1500—1650 | 440—630 |
7,25—3,4 |
425—600 |
9,45—4,9 |
МДК-3 | Cu—8,1—12Mo | 9,05—9,1 | 0,024—0,028 | 1650—1800 | 635—785 |
3,25—1,8 |
605—730 |
4,85—3,9 |
Установлено влияние шероховатости поверхности подложки на морфологию поверхности и особенности структуры конденсата в его сечениях. Для молибден-медного конденсата свойственна слоистость с иерархией макро-,микро- и субмикроуровней и различной структурой слоев. При этом для слоев, обогащенных медью, характерна преимущественно изотропная структура, состоящая из разориентиро- ванных полигональных зерен (рис. 3, а) либо из частиц сфероидальной и чечевицеподобной форм, диспергированных в матрице на основе меди (рис. 3, б). Для слоев, обогащенных молибденом, характерна анизотропная (столбчатая) структура (рис. 3, в).
Изменение структуры и химического состава обусловлено особенностями изменения свойств (табл. 2). Увеличению содержания молибдена и повышению роли столбчатой структуры соответствует возрастание прочности и твердости, но снижение пластичности. Коммутационные испытания показали, что в таком градиентном материале изменения химического состава слоев могут ограничивать зону термического влияния разряда. У контактов из парофазных конденсатов в ряде типов коммутационных аппаратов наблюдаются меньшие объемы вторичной структуры (рис. 4), чему соответствует повышение стойкости по сравнению с порошковыми контактами.
Материалы МДК обладают рядом достоинств: их получают за один технологический цикл, они дешевле аналогов, получаемых методами порошковой металлургии (в 1,5—1,7 раза) и существенно (в ~4 раза) дешевле серебросодержащих контактов. По эксплуатационной надежности МДК не уступают материалам на основе серебросодержащих композиций. Выдерживают максимальную величину коммутационного тока до 1200 А. Материалы МДК хорошо обрабатываются резанием, штамповкой, шлифованием, сверлением, легко паяются любыми из известных способов пайки с использованием стандартных серебросодержащих и бессеребряных припоев.
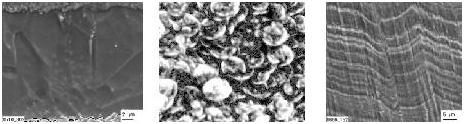
Рис. 3. Типичная структура КМ Cu—Zr—Y—Mo.
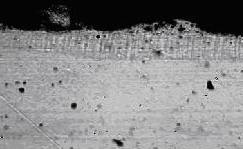
Рис. 4. Типичная структура внеш него слоя материала МДК-3 после коммутационных испытаний (х150).
Наиболее эффективные области применения МДК: городской транспорт (контакты, используемые в городских трамваях, троллейбусах, поездах, метро); лифтовое хозяйство (пассажирские и грузовые лифты); портовые, корабельные краны и другие подъемно-транспортные механизмы; электрокары всех типов; горно-шахтное оборудование; промышленные и бытовые электротехнические устройства, содержащие реле, пускатели, контакторы, рубильники и т. п.; междугородный электротранспорт (электровозы, тепловозы, электрички).
До настоящего времени произведено более 15 т электроконтактных материалов МДК, из которых изготовлено более 1,5 млн. шт. электрических контактов 376 типоразмеров в соответствии с техническими условиями Украины ТУ У 31.20113410-003-2002.
Общий вид разрывных контактов показан на рис 5, а. Композиционные материалы МДК успешно используются для изготовления скользящих контактов [31, 32]. Их экспериментальная и промышленная апробация осуществлена Вроцлавским политехническим институтом и Любинским медно-рудным предприятием (Польша). По долговечности указанные контакты превосходят контакты на основе углеродсодержащих материалов примерно в 8—12раз. Общий вид скользящего контакта показан на рис. 5, б.
Композиционные материалы на основе вольфрама и меди, изготавливаемые методами порошковой металлургии, традиционно используются в качестве сильноточных электрических контактов масляных, маломасляных, элегазовых выключателей, а в последнее время и некоторых типов вакуумных. Альтернативой порошковым материалам в последнем случае могут служить парофазные вольфрам-медные композиты. Проведены исследования композиционных материалов систе- мы Cu—Zr—Y—Wв интервале концентрации вольфрама 5—60% (мас.). При изучении Cu—Wкомпозиций установлено, что при конденсации на неподвижную подложку формируется градиентный слоистый материал, для которого характерна иерархия слоев с разнообразной структурой.
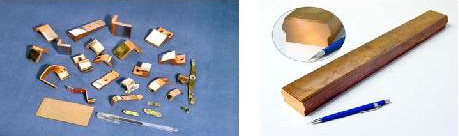
Рис. 5. Общий вид контактов: разрывных (а) и скользящего (б), изготовленных с применением материала МДК.
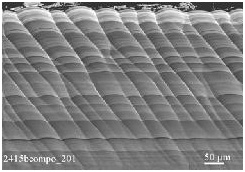
Рис. 6. Типичная структура конденсированных из паровой фазы КМ Cu—Zr—Y—Wс содержанием вольфрама 40— 60% (мас.).
В интервале содержания вольфрама 40—60% (мас.) в слоях преобладает столбчатая структура, нередко объединяющая слои не только различных иерархических уровней, но и все слои по толщине конденсата (рис. 6). Диаметр столбцов не превышает 100 мкм. Материал столбцов является композиционным с размером частиц вольфрама в матрице на основе меди менее 1 мкм. Таким образом, парофазный конденсат на основе вольфрама и меди является слоистым, градиентным с реализацией эффекта дисперсного упрочнения.
Изменение свойств конденсированного вольфрам-медного материала в исходном и отожженном состояниях при испытании на растяжение в зависимости от содержания вольфрама показано на рис. 7. Как видно на рис. 7, механические свойства КМ Cu—Zr—Y—Wповышаются в диапазоне концентраций вольфрама 35—55% (мас.). Вакуумный отжиг приводит к некоторому снижению прочности и увеличению пластичности.
Для электрических контактов вакуумных дугогасительных камер применяют материалы Cu—Cr с содержанием хрома 35—50% (мас.). Возможность использования конденсированных КМ в этой системе обусловлена особенностями химического состава и морфологии вторичной структуры, образующейся на рабочей поверхности порошковых контактов уже при тренировке вакуумных дугогасительных камер. В неравновесных условиях воздействия дугового разряда в рабочем слое увеличивается взаимная растворимость меди и хрома и происходит распад твердых растворов с формированием дисперсной структуры. То же наблюдается в конденсате на основе меди и хрома. Конденсаты Cu—Zr—Y—Cr в исходном состоянии при этом содержании хрома имеют слоистую структуру с иерархией размеров этих слоев: присутствуют слои макро-, микро- и субмикроуровней. Последние два уровня объединяются анизотропией нормального роста, способствующей формированию столбчатости в пределах нескольких слоев конденсата (рис. 8).
Широкая концентрационная область существования столбчатой структуры позволяет сделать предположение о единой природе массопереноса в этой области и сильно неравновесном характере материала конденсата. Действительно, под воздействием температуры и времени в сечении слоя, перпендикулярном столбцам, образуется зеренная, полигональная структура (рис. 9, а) с признаками распада пересыщенного твердого раствора (рис. 9, б).
Измерения твердости по Виккерсу в зависимости от содержания хрома показали ее линейный характер в пределах концентрации0—70% (мас.). При концентрации 35—50% Cr твердость изменяется в пределах 2069— 2503 МПа. При испытании на растяжение предел прочности увеличи- вается, до 550 МПа при содержании 40% (мас.) хрома, однако пластичность при этом падает.
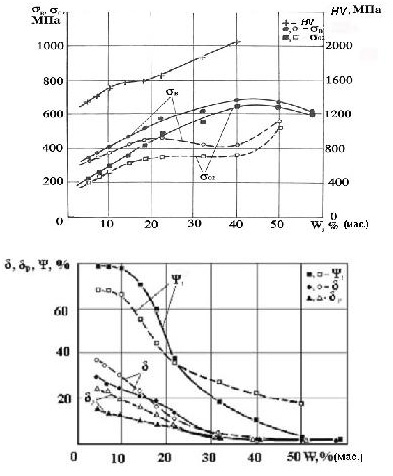
Рис. 7. Влияние содержаниявольфрама напрочностные (а) и пластические (б) характеристики конденсатаCu—W:испытание при комнатной температуре. Сплошные линии и темные точки — исходное состояние; штри- ховые линии и светлые точки — отжиг при 900 °С, 1 ч.
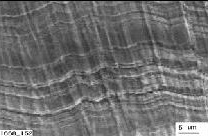
Рис. 8. Типичная структура конденсированного из паровой фазы КМCu—Zr—Y—Cr с содержанием хрома 35—50% (мас.).
Изучены структурные особенности разрушения при испытаниях на растяжение. Установлено, что основным типом разрушения является интеркристаллитный. Его роль возрастает при увеличении содержания хрома и количества источников разрушения (надрезов на поверхности образцов, дефектов на границах раздела в материале, обусловленных наличием примесей в нем). Композиционные материалы систем Cu—Zr—Y—W и Cu—Zr—Y—Cr используются для изготовления контактов дугогасительных камер [33—35].
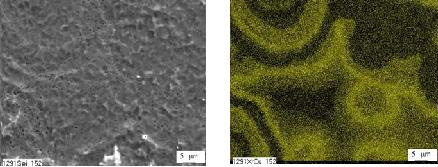
Рис. 9. Особенности структуры КМCu—Zr—Y—Crс содержанием хрома 35—50% (мас.): а — зеренная полигональная структура во вторичных электронах; б — признаки распада пересыщенного твердого раствора; изображение в рентгеновских лучах меди.
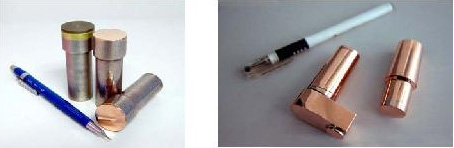
Рис. 10. Рис. 11. Общий вид контактов для дугогасительных камер и электродов для контактной сварки.
Проведена промышленная апробация технологии изготовления комбинированных контактов из конденсированных материалов на основемеди и вольфрама (хрома) на предприятии “Элтехмаш” (Украина). Вроцлавским политехническим институтом (Польша) осуществлено апробирование коммутационной стойкости таких контактов. Результаты положительные. Общий вид контактов для дугогасительных камер представлен на рис. 10.
Начата экспериментальная апробация электродов для контактной сварки на базе материала Cu—Zr—Y—Al2O. Общий вид этих электродов представлен на рис. 11.
Таким образом, приведенные данные свидетельствуют о возможности широкого применения альтернативного порошковой металлургии электронно-лучевого метода получения КМ дляэлектрических контактов. Указанный метод позволяет конструировать материал на атомно-молекулярном уровне с заданной дисперсностью ираспределениемфаз по его толщине.
Электронно-лучевая технология является абсолютно экологически чистой, так как при производстве материалов не происходит никаких вредных выбросов в окружающую среду.
Предложенный метод является более экономичным по сравнению с методами порошковой металлургии, поскольку получение материала осуществляют за один технологический цикл.
Современное электронно-лучевое оборудование позволяет получить до 15 т конденсированных композиционных материалов, из которых можно изготовить около 800 000 тыс. электрических контактов и электродов различного назначения.
1. Зуев И. В. Обработка материалов концентрированными потоками энергии. — М.: МЭИ, 1998. — 162 с.
2. Технология тонких пленок: (Справ.) / Под ред. Л. Майселла и 3. Гленга. — М.: Сов. радио, 1997. — Т. 1.— 662 с. — Т. 2. — 764 с.
3. Ройх И. Л., Колтунова Л. Н. Защитные вакуумные покрытия на стали. — М.: Машиностроение, 1997. — 297 с.
4. Самсонов Г. В., Эпик А. П. Тугоплавкие покрытия. — М.: Металлургия, 1973. — 398 с.
5. Шиллер З., Гайзиг Г., Панцер З. Электронно-лучевая технология. — М.: Энергия, 1980. — 528 с.
6. Мовчан Б. А., Малашенко И. С. Жаростойкие покрытия, осаждаемые в вакууме. — К.: Наук. думка, 1983. — 230 с.
7. Повышение качества поверхности и планирование металлов: (Справ.) / Под ред. А. Кушнера. — М.: Металлургия, 1984. — 376 с.
8. Bunshah R. F. Vacuum eveporation — history Recent developments and application // Zeitschrijt jur Metallkunde. — 1984. — 75, No. 11. — P.840—846.
9. Мовчан Б. А. Неорганические материалы, осаждаемые из паровой фазы в вакууме // Современное материаловедение в ХХІ веке. — К.: Наук. думка, 1998. — С. 318—332.
10. Косторжицкий А. И., Лебединский О. В. Многокомпонентные вакуумные покрытия. — М.: Машиностроение, 1987. — 207 с.
11. Ильинский А. И. Структура и прочность слоистых и дисперсно-упрочненных пленок. — М.: Металлургия, 1986. — 140 с.
12. Францевич И. Н. Электрические контакты, получаемые методом порошковой металлургии // Порошковая металлургия. — 1980. — № 8. — С. 36—47.
13. Раховский В. И., Левченко Г. В., Теодорович О. К. Разрывные контакты электрических аппаратов. — М.: Металлургия, 1966. — 295 с.
14. Спеченные материалы для электротехники и электронники: (Справ.) / Под ред. Г. Г. Гнесина. — М.: Металлургия, 1981. — 343 с.
15. Минакова Р. В., Грекова М. Л., Кресанова А. П., Крячко Л. А. Композиционные материалы для контактов и электродов // Порошковая металлургия. — 1995. — № 7/8. — С. 32—52.
16. Тучинский Л. И. Композиционные материалы, получаемые методом пропит- ки. — М.: Металлургия, 1998. — 206 с.
17. Композиционные материалы: (Справ.) / Под ред. Д. М. Карпиноса. — К.: Наук. думка, 1985. — 591 с.
18. Материалы в приборостроении и автоматике: (Справ.) / Под ред. Ю. М. Пятина. — М.: Машиностроение, 1982. — 527 с.
19. Leis P., Schuster K. K. Der еinjlus des kontactmaterials auf die austildundvon plasmastrahlen // Elekctric. — 1979. — 33, No. 10. — S.514—516, 559.
20. Мовчан Б. А.,Гречанюк Н. И. Новые материалы и покрытия, получаемые по электронно-лучевым технологиям: Сб. трудов ЭЛТ-88 (31 мая—4 июня 1988 г., Варна, Болгария). — Варна, 1988. — С.1005—1023.
21. Фаткуллин О. Х. Новые конструкционные порошковые материалы и их применение // Итоги науки и техники. Порошковая металлургия. — М.:ВИНИТИ, 1991. — Т. 5. — С.140—177.
22. Минакова Р. В., Кресанова А. П., Гречанюк Н. И. Композиционные материалы для контактов и электродов. Материалы на основе Мо // Электрические контакты и электроды. — К.: Ин-т пробл. материаловедения НАН Украины, 1996. — С. 95—105.
23. Slade P. E. Arc erosion oj tungsten based contacl materials. A review // Internat. J. of Refractory and Hard Metals. — 1986. — 5, No. 4. — P.208—214.
24. Двойные многокомпонентные системы на основе меди / Под ред. Н. Х. Абрикосова. — М.: Наука, 1979. — 35 с.
25. Mackey T., Ziolkowski I. Subsolidns phase diadram of Cu2O—CuO—MoO system // J. Solid. Stat. Chem. — 1980. — No. 31. — Р.135—143.
26. Mackey T., Ziolkowski I. Phase relatioh in the cupric molibdates — cuprous molibdates gystem // Ibid. — Р.145—151.
27. Гречанюк И. Н., Гречанюк В. Г., Емельянов Б. М., Руденко И. Ф. Коррозия композиционных материалов на основе меди, используемых для электрических контактов // Электрические контакты и электроды. — К.: Ин-т пробл. материаловедения НАН Украины, 1998. — C. 140—144.
28. Гречанюк Н. И., Осокин В. А., Гречанюк И. Н. и др. Композиционные материалы на основе меди и молибдена для электрических контактов, конденсированные из паровой фазы. Структура, свойства, технология. Часть 2. Основы электронно-лучевой технологии получения материалов для электрических контактов // Современная электрометаллургия. — 2006. — № 2. — C.9—19.
29. Пат. 34875 України. Композиційний матеріал для електричних контактів та спосіб його отримання / М. І. Гречанюк, В. О. Осокін, І. Б. Афанасьєв, І. М. Гречанюк. — Опубл. 16.12.2002 р.
30. Пат. 74155 України. Спосіб отримання мікрошаруватих термостабільних матеріалів / М. І. Гречанюк. — Опубл. 15.11.2005 р.
31. Miedzinski B., Wisniewski G., Shoffa V. N., Grechanyuk N. I. Performance of copper-molibdenum contacts when used for inductive DC load // Электрические контакты и электроды. — К.: Ин-т пробл. материаловедения НАН Украины, 2004. — С. 19—23.
32. Miedzinski B., Wisniewski G., Godzinski A. et al. Erosion of copper-molibdenum composition under DC load of a small power // Там же. — C. 23—28.
33. Пат. 32368А України. Контактний матеріал для дугогасних камер та спосіб його отримання / М. І. Гречанюк, М. М. Плащенко, В. О. Осокін, І. Б. Афанасьєв, І. М. Гречанюк. — Опубл. 15.12.2000 р.
34. Пат. 76737 України. Контактна система вакуумної дугогасної камери / М. І. Гречанюк, М. М. Плащенко, А. В. Зварич, В. О. Осокін. — Опубл. 15.09.2006 р.
35. Пат. 86434 України. Композиційний матеріал для електричних контактів і електродів та спосіб його отримання / М. І. Гречанюк, І. М. Гречанюк, В. О. Денисенко, В. Г. Гречанюк. — Опубл. 27.04.2009 р.