Structure, properties, technology. Part 1.
State-of-the-art and prospects of application of technology of electron beam high-rate evaporation-condensation for producing materials of electric contacts
N.I. GRECHANYUK, V.A. OSOKIN, I.N. GRECHANYUK and R.V. MINAKOVA
The grounds are given for the selection of composition, structure and technology of producing the composite materials on base of Cu-Mo system using the method of electron beam high-rate evaporation-condensation. The peculiar features of the technological process and equipment for its realization are shown. Results of examination of structure of vapor-phase composite materials on copper and molybdenum base, their properties, comparative data about the behavior of materials of different origin (powdered and condensed) under the conditions of arc discharge action are given. Expediency of selection of vapor-phase composite materials was substantiated as an alternative of cermet materials with account for the experience in the development and application of powdered composite materials as electric contacts.
Keywords: composite materials, powdered metallurgy, electron beam evaporation-condensation, electric contacts
Evaporation and subsequent condensation of materials in vacuum is the comparatively young trend in the materials science. It is connected with the use of physical-technological properties of electron beam [1], characterized by the highest effectiveness in metal treatment as compared with other known concentrated power flows (laser, plasma). Electron beam has the highest coefficient of power absorption. The range of power and energy concentration in the beam are significant (power of electron beams of 1 MW and more). In this connection the material heating up to the preset temperature, melting, evaporation are proceeding at very high rates. This beam features, used in metal treatment in vacuum, reduce the feasibility of their contamination with impurities, make the electron beam a perfect power source in metal treatment [1], Electron beam high-rate evaporation with a subsequent condensation in vacuum is one of the constituents of the process used in producing fine (up to 5 micron) films for radio engineering, micro electronics, computer engineering, etc. [2, 3], as well as thick films (more than 5 micron), used as effective protective and wear-resistant coatings [4-9],
The prediction estimate of the world production of metallic materials using different groups of technological processes (traditional metallurgy and deposition from vapor phase, including thin films, produced by the magnetron sputtering of metallic targets) until 2010 shows the further growth of new materials produced by the method of deposition of the vapor phase in vacuum [10].
Creation of multi-component coatings, designed for improving the electro-erosion resistance of electric contacts of commutation apparatuses, is promising. The scientific and industrial experience, gained in the development of similar coatings, is generalized most comprehensively in manuscript [11]. A special attention is paid here to the coatings from alloys on the base of copper, alloyed with tin, chromium, aluminium, nickel and titanium. Coatings were deposited on the prefabrications of products by evaporation of final weighed quantities. It was established that the coatings of Cu-Sn systems increase the serviceability of contact-parts of variable non-wire composite resistors, while Cu-Cr-Al systems increase the serviceability of cermet resistors.
The work [12] outlines the feasibility of use of high-strength films of Cu-0.5 % AI2O3 system as coatings of electric contacts. It is important to emphasize that the coatings, deposited in vacuum, are much superior to the corresponding galvanic coatings by the level of wear resistance, in particular its temperature stability.
In spite of evident advantages, the vacuum coatings are not justified from the economic point of view, as the vapor utilization factor in coating deposition does not exceed usually 20 %. From the other hand, the insuperable difficulties are encountered in evaporation from one source of materials on the base of copper or silver with additions of refractory metals of tungsten, molybdenum, tantalum, niobium, zirconium, hafnium in either ratio, due to difference in pressure of components vapors. Due to impossibility of evaporation of multi-component materials at high rates, significant irreversible losses in evaporation, the competitiveness of methods of powder metallurgy in manufacture of composite materials (CM) with a metallic matrix of type of pseudo-alloys for medium- and heavy-loaded commutation hardware has been preserved.
In Ukraine, the development of CM for electric contacts using the methods of powder metallurgy was started at the end of the 1940s under the supervision of I.N. Frantsevich, whose results are summarized in work [13] and further developed more comprehensively by his pupils [14-18], Technological peculiarities of producing materials for electric contacts, their service characteristics and field of application are outlined in detail in publications [15-19].
In spite of opportunity of rather wide selection of materials for electric contacts of different purposes the problem of creation highly-reliable electric contacts has not been yet solved completely, as the requirements specified for the material of contacts, depend on the type of commutation (switching) apparatus and are changed with its updating and replacement by the new one. These requirements can be satisfied by the materials characterized by an optimized structure and appropriate complex of electric, chemical, mechanical and other properties, providing preset electric erosion resistance, service life and reliability of contacts.
The determinant effect on service characteristics of materials has a structure factor. The electric erosion resistance of contact-parts is a structure-sensitive parameter. The rate of erosion of contact-parts, made from CM W-Cu, depends, for example, on content of micropores: slightly — at content of pores up to 2 %, it is increased at 2-4 % and increased abruptly at above 4 % of pores [16, 20], The electric erosion resistance of high-current contacts of CM on the same base depends on dispersity of a refractory constituent which is optimized in accordance with a commutating current. For currents exceeding 1000 A, it is recommended to use the contact-parts, made from CM W-Cu, whose mean size of particles is not less than 20 micron [21], The increase in electric erosion resistance of medium-loaded and low-current contacts from CM in Ag-Me, Ag-MeO systems promotes, with increase in their dispersity, the decrease in intensity of plasma flows [22], Highly-dispersed CM on the silver base with addition of nickel and cadmium oxide are used widely in industry [15],
Contacts KMK-A10 and KMK-A20, manufactured from powders on the base of silver in Ag-Me, Ag-MeO systems, produced by the method of chemical deposition, have 1.5-2 times higher wear resistance and service life than the contacts from powders made using a mechanical mixing [19],
The use of the high-rate electron beam evaporation and condensation of metals and non-metals for the formation of coatings on the working surface of contacts and producing of massive condensed CM for electric contact represents a significant scientific and practical interest. Laboratory samples of CM of thickness up to 1-12 mm of dispersion-strengthened and microlayer types are investigated at the E.O. Paton Electric Welding Institute of the NAS of Ukraine since 1970s [23], Royal Aviation Research Institute of Defence Ministry of Great Britain [24] and in a number of other research laboratories. However, there is no information about the serial production of these materials.
Before commencing the development of the industrial electron beam technology of CM production for electric contacts it was necessary to solve a number of applied and research problems, one of them being economy. As to the cost, the electric contact materials produced by the method of evaporation and subsequent condensation of metals and non-metals in vacuum should be comparable with similar materials produced by the powder metallurgy. Development and use of CM, not containing noble metals, represents the most interest. By the service reliability the condensed electric contact materials should not be inferior to sintered powdered compositions. For this, it was necessary to solve the problems of selection of compositions and structure of electric contact materials, study of their physical-mechanical and service characteristics, working out of recommendations and creation of reproducible industrial technology of producing condensed CM.
Materials, produced by the methods of powder metallurgy without noble metals, are widely spread in the manufacture of contacts of commutation apparatuses. These are contacts on the base of tungsten and copper (KMK-B25, KMK-B45), molybdenum and copper (KMK-BMo50) KMK-BMo80) [15, 25], Powdered CM of these grades contain 20-80 wt.% of a refractory constituent; 0.5-12 wt.% of alloying elements (nickel, cobalt, silver, etc.), and also functioning additions. These compositions provide a good wetting and feasibility of producing structure of matrix and frame-matrix types. CM with approximately 50 and 70 % W (Mo), more often used in industry, have a structure of a matrix type with conglomerates, chains or separate grains of refractory constituent, dispersed in grains-colonies of the matrix. Such nature of the structure of main components and a phase composition of an easily-melting constituent, depending on the nature of alloying elements, have an influence on electric resistance, mechanical (hardness, resistance to bend, to tension within the range of temperatures 196-600 °C) and chemical properties (resistance to high-temperature oxidation at 20-800 °C) [16, 25], Contacts from these CM in medium- and heavy- loaded switches close and open the electric circuits under different conditions: in air, in oil, SF6 gas, vacuum, etc. [14, 26, 27].
Figure 1. Dependence of rate of electric erosion (a) and coefficient of electric transfer (b) on current for contacts from copper (1, 5), CM Mo-30Cu (2, 6), W-30Cu-3Ni (3, 7), Wo-50Cu-2Ni (4, 8)
In air, oil and SF6 gas switches the electroerosion wear of contacts is caused by the interaction of material of contact surfaces with hot, ionized, reactive gas flows.
In parallel with physical processes, proceeding under the action of electric arc, the chemical processes are proceeding on the working surfaces of contacts and in the inter-contact gap, promoting the occurrence of new compounds, the products of interaction of the contact material with a surrounding atmosphere.
Conditions of proceeding of chemical reactions in the given case are special, as the ionized gases, available in the composition of plasma of arc column and in the space surrounding it, and also vapors of materials of contacts are interacted. Products of interaction (oxides, carbides, nitrides, hydrides, sulphides, etc.), precipitated on the surface of contacts, form the more of less dense films, crusts and conglomerates, increasing the contact resistance of contacts. The negative action of the above-mentioned formations is decreased, if the compounds, available in their composition, are not stable, easily evaporated or brittle, having a non-dense abutting the contact surface, and are removed in closing of contacts, their mutual slipping or under the action of vapor-gas jets occurring in arc extinguishing. In this connection it is necessary to have a material for contacts of air switches, characterized by a high corrosion resistance, its oxides should be volatile, and the design of a contact unit should provide a feasibility of a mechanical «self-cleaning».
In use of contacts of W-Cu system, the oxides WO3 and Cu2O are the products of oxidation more often [19, 27]. Their specific resistance is varied within the wide ranges: for WO3 — from 1 (at a high deviation) up to 1-1012 Ohm/cm (at stoichiometric composition), and for Cu2O — from 1*103 up to 1*1010 Ohm/cm.
Peculiar features of service properties of high-current W-Cu contacts in operation in air are stipulated by a combined effect of processes of formation of secondary structure in a working layer under the action of arc discharge, its oxidation and destroying. It was established that when in the secondary structure composition the liquid phase is appeared, spreading along the working surface of contacts, the rate of electric erosion is reduced and a coefficient of ejection is stabilized (Figure 1) [16].
In current commutation in air the similar processes were also observed in a working layer of contacts made from pseudo-alloys Mo-Cu. Molybdenum and copper are dissolved in limits [28], while their oxides are interacted and form stable compounds (CuMoO4, Cu3Mo2O9 and others) [29. 30]. which promote the occurrence of easily-melted eutectics in MoO3-Cu2O system at temperature above 700 "C, leading to the decrease in corrosion at temperature more than 800 °C.
It was established that the oxide film, having a composition of eutectics or pseudo-eutectics in the MoO3-Cu2O system [29, 30], is easily spreading over the contact surface, filling roughness. By separating from the contact surface after crystallization due to a poor adhesion, the film promotes the effect of «self- cleaning» and reduction in level of a contact resistance of a contact pair [25].
Metals and CM, designed for operation in oxidizing media, protect from oxidation by alloying or deposition of coatings. In the coarse of investigation of CM of Mo-Cu system, the feasibility was establishment to increase their resistance to high-temperature oxidation in alloying by nickel and (to a less extent) by cobalt. It can be assumed on the basis of data of X-ray phase and X-ray spectral analyses that this difference is stipulated by the specifics of nickel and cobalt distribution in Mo-Cu system, their effect on the diffusion of oxygen and composition of products in heating in air within the temperature interval investigated [31].
Adding of carbon and lanthanum hexaboride into CM of Mo-Cu-Ni system contributes to the further increase in heat resistance. Additional weight of samples after oxidation in air at 700 °C temperature for 2 h was 260 mg/cm2 for Mo-Cu composition, and 42 mg/cm2 — for Mo-Cu-Ni-C-LaB6 composition. Except heat resistance, the CM of electric contacts purpose should satisfy the requirements to the level of hardness, strength, ductility, electro- and heat conductivity and other properties.
It was established in study of alloying effect on hot hardness of CM of W (Mo)-Cu system that the additions to increase the effectiveness can be arranged in the following sequence: Ni, Co, Ag, Zr, Ti, REM (La, Ce), Y, Zr (Ti)-REM [32], In the same sequence the temperature of beginning of softening of the above-mentioned compositions is increased by 200- 400 °C.
It was stated in producing materials by the method of electron beam evaporation-condensation of components and compounds, mutually insoluble or have limited dissolution in each other in liquid and solid state, that the level of mechanical properties depends on features of a contact interaction at the interphase, determined by a wetting angle by metallic melts of appropriate refractory metals and compounds [23].
If to use materials with an angle of wetting by matrix alloys of more than 90° as a strengthening phase for materials, condensed from a vapor phase, the pores-free materials cannot be produced due to formation of pores at the interphase [33]. Pores, forming in CM at such conditions, lead to an abrupt reduction in strength and electroerosion resistance [16]. The angle of wetting by a molten copper of tungsten and molybdenum in vacuum depends on the temperature of experiment and is, respectively, 50 and 12,18 and 4-5° at 1100 and 1250 °C [34],
Thus, to form CM on the base of copper it is possible to use molybdenum as a dispersed filler, except tungsten. Its advantages are stipulated also the lower temperature of melting (2614 for molybdenum and 3384 °C for tungsten) and higher vapor pressure at the temperature of melting. The increase in temperature of the molten pool hinders the CM producing by the method of a high-rate evaporation-condensation due to overheating and coming of order of copper crucibles, from which the evaporation of melts in industrial electron beam installations is realized [7]. The made analysis allowed us to select Cu-Mo system as a base in producing CM using a high-rate evaporation-condensation. Coming from the peculiarities of effect of additions on electric conductivity of alloyed alloys on copper base [15] and corrosion resistance of compositions Cu-Mo-Zr, Cu-Mo-Y, Cu-Mo-Zr-Y [35], zirconium and yttrium were selected for additional alloying of CM on copper and molybdenum base to improve their functional characteristics.
In electric current commutation in molten and gas media, and also in vacuum for a time connected with a formation, burning and extinguishing of arc in an intercontact gap [14, 26], the intensive heat flow, electric, gas and hydrodynamic forces are acting on the surface of contacts, stipulating complex physical- chemical processes, proceeding in non-equilibrium conditions, and also destruction and failure of the working layer of these contacts. With increase in capacity of heat flow, the duration of thermal effect, for example, melting of material of contacts, exceeds the time of action of the arc heat source [26]. Under these conditions, the processes of melting, «sweating», displacement (under the action of plasma jet), ejection, evaporation of easily-melting constituent, and also the consolidation due to capillary forces of refractory constituent, formation of extended areas of the secondary structure are occurred. All this promotes the complete destroying of initial structure in the working layer during even the first cycle of current commutation, that is coordinated with the change in a coefficient of ejection (see Figure 1, b) [36].
Figure 2. Grid of microcracks formed as a result of thermal fatigue fracture of a working layer of contact made from CM W-Cu-Ni (x32)
At a rapid cooling, in particular with increase in current of the same single pulse, a system of defects is developed in the secondary structure in the form of cavities, pores, single microcracks, their grids (mosaics) in a consolidated (after sintering, fusion) layer on the base of a refractory constituent (Figure 2). Structural changes in the working layer at increase in voltage by explosion exciting of arc discharge copper wire [36] occur at lower values of pulse current [37], In this case, except «mosaics», formed by the system of cracks of thermal fatigue failure, the macrospalling of a working layer along the edge of contacts of a cylindrical shape (Figure 3, a), local explosion-like fracture (Figure 3, b), radial (grooving) entrainment (Figure 3, c), «scouring» of the working layer (in particular in current commutation in oil) (Figure 3, d) and others are observed.
Change in shape of contacts (cylindrical with a flat working surface for cylindrical with a semi-spherical working surface) avoids the crack formation along the edges, but does not prevent the susceptibility to thermal fatigue failure.
With increase in a commutating current the size of cells of «mosaics» and depth of cracks is growing. Under these conditions, the macrospalling of the working layer of contacts is possible. It is supposed that this catastrophic change in surface relief is occurred in the case when it is impossible for the thermal fatigue crack, initiated in the zone of a thermal effect of discharge, to be «entrapped» in the initial material of the working layer. In accordance with the equation of Griffith-Orvan-Irvin, this can be connected with a decrease in an effective surface energy of formation of cracks in initial material, for example, as a result of accumulation of impurities along the boundaries, including boundaries of grains-colonies [38], Thermal fatigue fracture, caused by specifics of structural- phase changes in a working layer, leads to a loss in serviceability of contacts as a result of increasing the contact resistance, overheating, welding of contacts.
Distinct features of the thermal fatigue of material under the effect of heat changes were observed by our [35-37] and foreign [21,"27] researchers. Nevertheless, the list of reference parameters of standard documentation is limited more often by chemical composition, density, electric conductivity, hardness at room temperature, and in some cases by tensile strength, impact strength of initial materials. Methodological difficulties of establishment of correlation ratios (including thermal resistance of initial and secondary structures) contribute to limiting of composition of reference parameters. Criteria of thermal resistance is the number of cycles of temperature change until the appearance of a crack or a complete fracture. Under the conditions of abrupt local heat changes, connected with a heat action of arc discharge, the thermal stresses are occurred, whose level can exceed the ultimate strength of the working layer material with a secondary structure.
Work [39] gives a parameter R, characterizing the resistance of materials against the action of thermal stresses: R = a(1 - u,)/Ea, where a is the limiting stress; is the Poisson factor; E is the modulus of elasticity at tension; a is the thermal expansion factor.
The limiting stress of CM is characterized by a local micro non-uniformity, stipulated by a shape, sizes, distribution of structural constituents [40], The non-uniformity of limiting stresses and strains, typical of initial and secondary structure, contributes to initiation, propagation of cracks in the working layer of contacts. In this connection, the service life of the electric contact, made from powdered and condensed CM will depend on the capability of the secondary structure to relaxation of stresses, occurring under the effect of arc discharge, and the capability of the initial structure to relaxation of stresses at the apex of crack, occurring in the secondary structure, and arresting of this crack. Both in the secondary and in the initial structures, the susceptibility to fracture at heat changes depends on the level of a free surface energy of the boundaries [38].
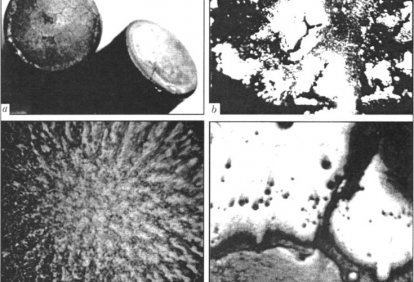
Figure 3. Peculiarities of failure of CM made from W-Cu-Ni: a — thermal fatigue failure and macrospalling of the contact working layer (x2); b — local explosion-like failure of the contact working layer (x32); c — radial (grooving) entrainment of the contact working layer (x32); d — brittle thermal fatigue failure and “scouring” of the contact working layer (x100)
Technology of a high-rate electron beam evaporation-condensation is an alternative to the powder metallurgy: a thermal dispersion of melt and consolidation of a dispersed flow of particles (without a special formation to produce a highly-dense state of material) with a liming content of impurities is attained in a single space. The peculiar feature of vapor-phase CM is their laminar structure with a gradient of chemical composition in thickness. In work [41] the more effective strengthening of CM was found with continuous fibers, as compared with discrete ones. Results of the present investigations are correlated with data of study of microlayer materials on the base of iron and copper, for which the more effective increase in strength, as compared with dispersion-strengthened materials of Fe-Cu system, was found [42], Microscopic elasticity limit, as one of the characteristics of strength of three-layer condensates Fe-Cu-Fe and Cu-Fe-Cu produced by electron beam evaporation and subsequent condensation in vacuum, depends on alternation of layers [43], These results prove the new dimensional factors of the structure influencing the properties of condensates.
Figure 4. Microstructure of HAZ in the contact working layer made from condensed CM on the base of copper and molybdenum: a — without etching; b — chemical etching (x100)
The preliminary investigations of effect of conditions of testing the electric contacts, made from vapor-phase CM on the base of copper and molybdenum, on the structure of the working layer showed that the change in chemical composition of layers can limit the discharge zone of thermal effect. In vapor-phase condensates, the smaller near-surface volumes of the secondary structure (Figure 4) and increase in resistance, typical of contacts made from CM, manufactured by the method of electron bean high-rate evaporation-condensation, as compared with powdered contacts, correspond to this in some types of the commutation apparatuses.
CONCLUSIONS
1. State-of-the-art of CM development using an electron beam as the most effective source of power in metal treatment was analyzed.
2. Results of investigation of powdered CM for electric engineering purposes (specifics of chemical processes of oxidation of CM of Cu-Mo system and effect of alloying elements on them) were presented to ground the selection of composition, structure and technology of manufacture of CM using the method of electron beam high-rate evaporation-condensation.
3. The role of structural changes under the conditions of effect of arc discharge is shown, peculiarities of thermal fatigue fracture of powdered CM in the working layer and its effect on serviceability of these contacts are established.
4. Peculiarities of heat-effect on the working layer of contacts, made from vapor-phase condensates, as well as the possibilities of limiting the zone of thermal effect of arc in the creation of laminar gradient vapor-phase CM are illustrated.
5. Prospects of application of vapor-phase CM as an alternative to powdered CM as contacts of commutation apparatuses are shown.
1. Zuev, I.V. (1998) Processing of materials by concentrated energy flows. Moscow: MEI.
(1977) Technology of thin films. Refer. Book. Vol. 1. Ed. by L. Maysell and Z. Gleng. Moscow: Sov. Radio.
2. Rojkh, I.L., Koltunova, L.N. (1971) Protective vacuum coatings on steel. Moscow: Mashinostroenie.
3. Samsonov, G.V., Epik, A.P. (1973) Refractory coatings. Moscow: Metallurgiya.
4. Schiller, S., Gajzig, H., Panzer, S. (1980) Electron beam technology. Moscow: Energiya.
5. Movchan, B.A., Malashenko, I.S. (1983) Vacuum-deposited high-temperature coatings. Kiev: Naukova Dumka.
(1984) Improvement of surface quality and cladding of metals. Refer. Book. Ed. by A. Kushner. Moscow: Metallurgiya.
6. Bunshah, R.F. (1984) Vacuum evaporation — history recent developments and applications. Zeitschrift fuer Met- allkunde, 75(11), 840-846.
7. Movchan, B.A. (1988) PVD inorganic materials. In: Current materials science in the 21st century. Kiev: Naukova Dumka.
8. Kostorzhitsky, A.I., Lebedinsky, O.V. (1987) Multicompo- nent vacuum coatings. Moscow: Mashinostroenie.
9. lliinsky, A.I. (1986) Structure and strength of laminated and dispersion-strengthened films. Moscow: Metallurgiya.
10. Frantsevich, I.N. (1980) Electric contacts made by powder metallurgy methods. Poroshk. Metallurgiya, 8, 36-47.
11. Rakhovsky, V.I., Levchenko, G.V., Teodorovich, O.K. (1966) Break contacts of electric apparatuses. Moscow-Leningrad.
(1981) Sintered materials for electrical engineering and electronics. Refer. Book. Ed. by G.G. Gnesin. Moscow: Metallurgiya.
12. Minakova, R.V., Grekova, M.L., Kresanova, A.P. et al. (1995) Composite materials for contacts and electrodes. Poroshk. Metallurgiya, 7/8
13. Tuchinsky, L.I. (1988) Composite materials produced by impregnation method. Moscow: Metallurgiya.
(1985) Composite materials. Refer. Book. Ed. by D.M. Karpinos. Kiev: Naukova Dumka.
14. Imm, R., Stempell, G. (1976) Der Einfluss der Poroesitaet auf einige Eigenschaften von W-Cu Kontaktwerkstoffen. Z. Werkstofftechnik, 7(1)
15. Gessinger, F.N., Melton, K.N. (1977) Burn-off of W-Cu contact materials in an electrical arc. Powder Metallurgy Int., 9(2), 67-72.
16. Leis, P., Schuster, K.K. (1979) Der Einfluss des Kon- taktmaterials auf die Ausbildung von Plasmastrahlen. Electric, 33 (10), 514-516, 559.
17. Movchan, B.A., Grechanyuk, N.I. (1988) New materials and coatings made by electron beam technologies. In: Proc. of ELT-88 Conf. (Varna,
Bulgaria, 31 May-4 June, 1988). Varna.
18. Fatkullin, O.Kh. (1991) New structural powder materials and their application. In: Results of science and technique. Powder metallurgy. Vol. 5.
Moscow: VINITI.
19. Minakova, R.V., Kresanova, A.P., Grechanyuk, N.I. (1996) Composite materials for contacts and electrodes. Mo-base materials. In: Transact,
on Electric Contacts and Elec...
20. Belkin, G.S. (2003) Commutation processes in electric apparatuses. Moscow: Znak.
21. Slade, P.G. (1986) Arc erosion of tungsten based contact materials. A review. Int. J. Refractory & Hard Metals, 5(4), 208-214.
(1979) Binary and multicomponent Cu-based systems. Refer. Book. Ed. by N.Kh. Abrikosov. Moscow: Nauka.
22. Mackey, T., Ziolkowski, I. (1980) Subsolidus phase diagram of Cu20-Cu0-Mo03 system. J. Solid. Stat. Chem., 31, 135-143.
23. Mackey, T., Ziolkowski, I. (1980) Phase relations in the cu- pric molibdates-cuprous molibdates system. Ibid., 145-151.
24. Minakova, R.V., Lesnik, N.D., Kresanova, A.P. et al. (1986) Contact interaction, structure and properties of molybdenum- copper-nickel (cobalt) composition. In: Adhesion of melts ana soldering of materials. Issue 17. Kiev: Naukova Dumka.
25. Minakova, R.V., Frantsevich, I.N., Lesnik, N.D. et al. (1979) Composite materials for high-current contacts and electrodes. In: Proc. of 5th Conf. on Powder Metallurgy in Poland. Vol. 2.
26. Eryomenko, V.N., Najdich, Yu.V., Lavrinenko, I.A. (1962) Sintering in presence of liquid metal phase. Kiev: Naukova Dumka.
27. Najdich, Yu.V. (1972) Contact phenomena in metallic melts. Kiev: Naukova Dumka.
28. Grechanyuk, I.N., Grechanyuk, V.G., Emelianov, B.G. et al. (1998) Corrosion of composite copper-based materials used for the electric contacts. In: Electric contacts and electrodes. Kiev.
29. Ignatko, V.P., Kukhtikov, V.A., Kresanova, A.P. et al. (1972) Comparative investigation of erosion processes on copper and cermet electrodes in high-current quasi-stationa- ry arc. In: Electric contacts (theory and application). Mos
30. Minakova, R.V., Flis, A.A., Kukhtikov, V.A. et al. (1977) Influence of conditions of discharge excitation on arc erosion of contacts. In: Electric contacts and electrodes. Kiev: Naukova Dumka.
31. Das, E.S.P., Marcinkowski, M.J. (1972) Accommodation of the stress field at a grain boundary under heterogeneous shear by initiation of microcracks. J. Appl. Phys., 43 (11), 4425-4434.
32. Tretiachenko, G.N. (1977) Heat resistance. In: Encyclopedia of inorganic materials. Vol. 2. Kiev: GRUSE.
33. Minakov, V.P., Polyakov, L.M., Tron, A.S. (1975) Mechanical properties of thin copper interlayers in compositions. Problemy Prochnosti, 10
34. Movchan, B.A. (1990) Dimensional-structural relationships of strength of two-phase inorganic materials. Preprint. Kiev: PWI.
35. Mogilnikova, T.T., Nerodenko, L.M., Movchan, B.A. (2002) Microscopic limit of elasticity of two-phase Cu- 68 vol.% Fe material produced by electron beam physical vapor deposition in vacuum. Advances in Electrometallur- gy, 2,16-17.
36. Mogilnikova, T.T., Nerodenko, L.M., Movchan, B.A. (2004) Microscopic limit of elasticity of three-layer material of Fe-Cu system deposited from vapour phase. Ibid., 1, 15-16.